Type 31
Delivering the next generation of warships
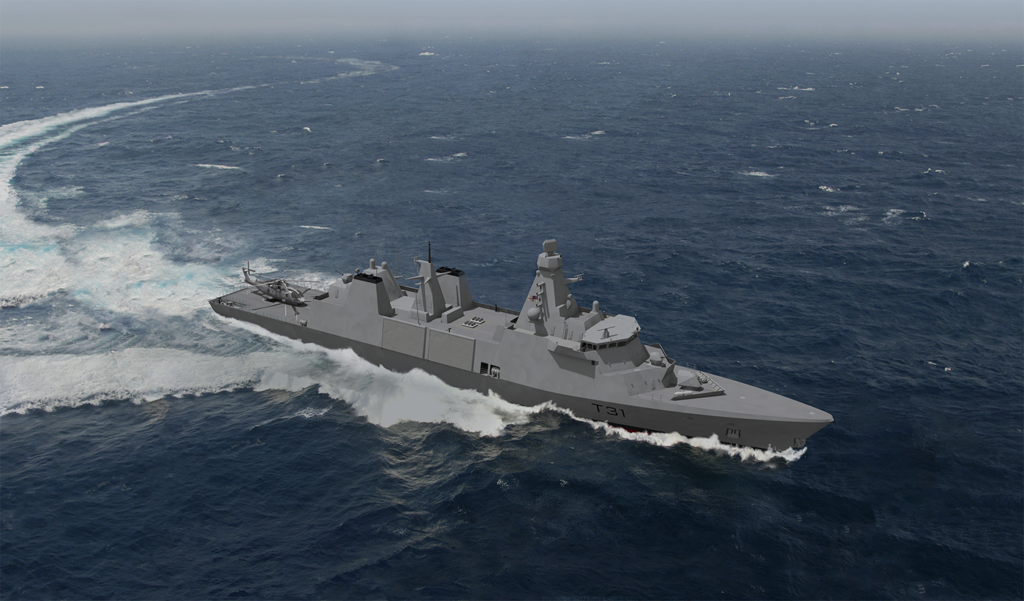
Creating a safe and secure world has never been more important.
We support the Royal Navy’s mission to deter aggression and maintain the security of the UK’s interests by delivering the next generation of Royal Navy warships, the Type 31 general purpose frigates.
Awarded to Babcock in November 2019, this contract to deliver five Type 31 general purpose frigates, signalled another decade of ship-build activity for the historic dockyard at Rosyth, one of the largest waterside manufacturing and repair facilities in the UK.
Building on the unique experience and success of the Aircraft Carrier Alliance, we have brought together a highly experienced and integrated project team spanning several regions of the UK, to meet the challenging Type 31 programme.
Re-energising the UK’s maritime capability through modern UK ship design and build practices, the Type 31 programme is the first of its kind to be delivered under the new National Shipbuilding Strategy. The innovative programme will strengthen technology transfer into the UK and drive British shipbuilding expertise to deliver the Royal Navy, a world leader in naval platforms, the ‘Inspiration’ class.
The Type 31 will be at the heart of the Royal Navy’s surface fleet, working alongside the UK’s Allies to deliver a UK presence across the globe.
At a glance:
- HMS Venturer – steel cut in 2021
- HMS Venturer – keel laying 2022
- HMS Active – steel cut in 2023
- HMS Active – keel laying 2023
- HMS Formidable – steel cut in 2024
Type 31: A state-of-the-art warship
A state-of-the-art warship, the Type 31 has been engineered to meet the challenges of the future maritime environment. Assembled at our Rosyth facility, the programme maximises prosperity throughout the UK maritime supply chain. As part of ongoing investment at Rosyth, the newly built Assembly Hall is dedicated to the Type 31 programme and provides a modern, future-ready facility designed to assemble two vessels side by side. Free from weather disruption, the facility enables productivity gains due to improved access and digital connectivity.
Digital transformation is at the heart of our delivery of Type 31. This is not just a vision for the future, but it is now a reality throughout the Type 31 programme, where investment is enabling integration of technology, knowledge and production. With new working practices, we have created a dynamic, effective and efficient, digitally enabled shipbuilding capability. A digital thread runs through design, procurement, build and will be available for use through the life of the Type 31s.
A proven, capable and adaptable frigate for global navies
A key element of the Type 31 programme is to supply a design with the potential to secure a range of export orders supporting the UK economy and jobs. Arrowhead 140, the base design of the Type 31, offers export customers an unrivalled blend of efficiency, capability and flexibility backed by world-class experience.
We can provide a UK build strategy that offers flexibility around programme requirements and capacity. We offer a range of export strategies to maximise local in-country content through design, technology and knowledge transfer.
Find out moreType 31 in numbers, across the duration of the programme:
- £100m infrastructure investment at Rosyth over the past decade to modernise the dockyard for Queen Elizabeth Carriers and Type 31
- £55m additional investment in advanced systems technologies at Rosyth now underway
- 1,250 strong workforce throughout the UK at the peak of the programme, plus an additional…
- …1,250 within the wider maritime supply chain
- 150 new apprenticeships across the UK 5 state-of-the-art general purpose frigates delivered to the Royal Navy